液晶や半導体などの製造現場を陰で支えているのが産業機械である。三菱電機はこの産業機械部門で、品質改善 活動に取り組んでいる。柱は、製造工程の「見える化」だ。それを実現するために製造設備をネットワークでつなぐ「e-F@ctory」を構築した。不良品 による品質ロスが半減するなど効果が出ている。
トヨタ流改革など業務改善に挑む企業がこぞって取り組むのが「見える化」だ。整理整頓などによって改善すべきポイントを見つけやすくするものだ。 見える化を進めるには、まずは現状把握が必要になる。「在庫」のように定量的に測れればよいが、製造ラインや製造設備といったものだと容易ではない。担当 者がストップウオッチ片手に各工程に張り付くなど現状把握するだけでも人手と時間がかかってしまう。
この難題を克服し、「製造状況の見える化」で成果を上げているのが、三菱電機の産業機械部門である。2003年から名古屋製作所で取り組んでいる 「e-F@ctory」がそれだ。簡単にいえば、各工程の製造設備が正常に稼働しているかどうかといった情報をリアルタイムで収集するものである。
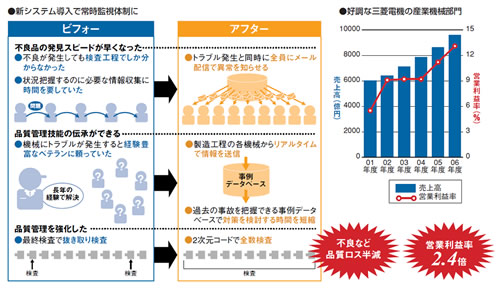 |
●新システム導入で常時監視体制に [画像のクリックで拡大表示] |
e-F@ctoryを導入したのは、同製作所の主力製品であるサーボモーター。液晶や半導体関連のメーカーが使うもので、高い性能が求められる。例えば、液晶の薄膜を塗布する工程では、ミクロン単位で位置が決められるサーボモーターの制御性能が問われる。
サーボモーターの優劣を決めるのは、制御の精度である。モーターに巻きつけるコイルの着磁状況がその鍵となる。ごく小さな回転ムラでも、発生する磁界にばらつきを生んでしまい、高精度な制御ができなくなってしまう。
サーボモーターの性能が悪ければ、ユーザー企業の製造計画にも大きな影響を与える。サーボモーターが製造停止の原因となれば賠償請求を受けかねな い。停止時間など影響を受けた度合いを算出され、億円単位の損害賠償でさえあり得るのだ。三菱電機にとっては、製造不良は許されない。万が一不良があった としても、出荷前に何とか食い止める仕組みが必要だった。
製造設備の制御通信網を活用
これまで同社では、不良を発見するために、最終検査工程で動作確認などを入念に実施するとともに、各工程でも抜き取り検査で品質に目を光らせてい た。だが、最終検査で不良を発見しても、どの工程が問題だったのかはすぐには分からず、手を施しづらかった。再発を防ぐため、根本的な原因がどこにあるの かを突き止めるのに2~3日間かかることもあったという。
同様に製造工程のムダを改善しようとする場合でも、どこに課題点があるのか把握しづらかったという。担当者が各工程の製造設備のそばでストップウ オッチ片手に数週間張り付いてデータを収集していた。「知恵をひねる以前に、事前準備に多大な労力がかかっていたのが実態だった」とe-F@ctory技 術企画の渡部裕二グループマネージャーは振り返る。いくら改善のアイデアが思い浮かんでもその検証に時間がかかってしまっていた。
不良の発見においても工程のムダ取りにおいても、人手による限界を感じていた渡部グループマネージャーらが注目したのが、工場内に張りめぐらせて あるネットワークだった。通信装置を取り付けたレーザー加工機や産業ロボットをつないで制御するための、「MELSECNET」と呼ぶ通信網である。
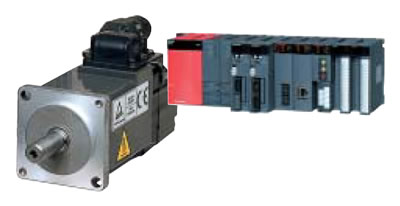 |
名古屋製作所で製造するサーボモーター(左)と、製造設備から状況を送信するための通信装置(右) |
この通信網は1980年代から使用しているが、機械を制御するためだけに活用していた。だが発想を変えれば、品質改善にも活用できることに気づい た。「機械を制御する」という一方向だけでなく、「制御した実績情報」という逆方向の情報を収集する。すべての製造設備から情報収集することで、リアルタ イムに監視できている状態となり、「製造工程の見える化」が実現できると渡部グループマネージャーらは考えたのだ。
まず機械加工工場に試験導入した。情報収集の容易さといった効果を担当者が実感できたため、サーボモーターなど特に品質管理が厳しい名古屋製作所の3工場への導入に踏み切った。
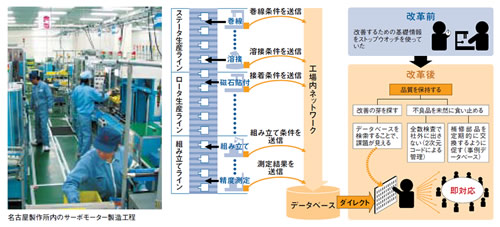 |
●新システム導入でサーボモーターの製造状況を「見える化」 [画像のクリックで拡大表示] |
サーボモーターの製造工程にある主な製造設備からは、コイルの巻き線条件や抵抗値、ボルトを締め付けた際の圧力といった製造実績に加えて、各工程の検査結果情報を吸い上げていく。情報の吸い上げポイントは200カ所に及ぶ。
過去のトラブルをデータベース化
こうして集めた情報を、不良を発見してから解決策を立てるまでの時間短縮に活用する。各製造設備から届く実績が、あらかじめ設定した基準値を外れ ていると、事務棟などばらばらの場所にいる関係者全員に同報メールで一斉に知らせるとともに、問題が発生した設備に赤いランプが点灯する。これまではライ ンリーダーから班長へ報告といったバケツリレー方式での情報伝達だった。
製品には、200カ所から届いた情報を2次元コードにして張っておく。不良が発生した際に、どの製造設備が原因だったのかをさかのぼって把握するためだ。原因究明の手がかりとなる。
不良の原因を究明するうえで効果を発揮するのが、事例データベースである。過去のトラブル発生状況と、その解決法を登録。発生事象別に類型化して検索しやすくしたものだ。このデータベースを検索することで、おおよその原因の見当がつき、対策に早く動ける。
例えばハンダ不良によるトラブルが発生したとする。データベースを検索することで、過去に発生した類似のケースが見つかる。そのケースによると、 ハンダ漕の温度管理機能が機能していないことが原因だった。今回も同様の疑いがあるので、ハンダ漕を確認することから始められるといった具合だ。これまで は熟練の担当者に聞いて判断を仰ぐなど属人化していた。
品質トラブルを未然に防ぐ
原因究明する過程でも、e-F@ctoryで関係者全員に発生状況を共有できていることが役立つ。各ラインには製造計画があり、停止時間が長引くほど計画の達成が困難になってしまうから不良情報への関心は高い。
新システムにより、製造計画の達成に責任を持つ課長クラスまで現場の状況が共有できている。原因究明に時間をかけるべきか、ほかの品目に切り替え るべきかといった意思決定を早くできる。「現場はどうしても自分たちで何とかしようとしてしまう。責任者まで情報を共有できることで早く決断できるように なった」と渡部グループマネージャーは話す。
品質トラブルを未然に防ぐうえでも、e-F@ctoryが役立つ。その1つが、治具や工具の交換時期を通知する機能である。早く交換し過ぎてしま えば効率が悪く、適切なタイミングを逸すると不良品を発生させる危険がある。これまでは熟練工の経験と勘に頼っていたため、タイミングがまちまちだった。 各製造設備から実績に加えて金型や治具の使用回数も送られ、これらをデータベースに蓄積している。あらかじめ交換周期といった条件を設定しておくことで、 担当者に通知する。適切なタイミングで確実に交換できるようになった。
治具などの使用回数も含めた製造設備からの実績を、改善活動のヒント探しに生かす。トラブルが発生する前に先回りして課題を見つけ、改善策を講じ るためだ。データベースには、担当者が現場で長期間ストップウオッチで測らなくても基礎情報が集まっている。「各製造設備における総停止時間のワースト 3」といったように、様々な角度から検索できる。何を優先課題とすべきなのかが明確になる。課題が見えているので、どう解決するかという本質的な改善活動 へすぐに取り掛かることができる。
例えば、停止時間が多い設備は、製造設備の問題なのか、工程に課題があるのかなど具体的に議論が進められる。工程であれば、標準時間の見直しなど製造設備の停止時間を短縮するための対策を立案できる。
これらの取り組みにより、不良品にかかる費用など品質ロス(金額換算)が半減するとともに、設備稼働率は190%に向上した。品質と生産性の両面を同時に向上させることに役立った。
こうした名古屋製作所での成果を受けて、三菱電機のほかの製造拠点にも導入していく。今年度をメドに自動車部品を製造する姫路製作所や冷蔵庫など白物家電を製造する静岡製作所でも取り組んでいく予定だ。
沒有留言:
張貼留言